Desarrollado por una candidata a doctorado en el Block Research Group de la Escuela Politécnica Federal de Zúrich, este nuevo encofrado liviano y reutilizable aprovecha una su particular geometría para la fabricación de pisos de hormigón de una manera sostenible con el medioambiente.
Fuente: Hormigón al día
Uno de los aspectos clave que hacen del hormigón el material para la construcción más usado en el mundo es que su producción es económica: sólo se necesita agua, áridos -finos y gruesos- y el cemento crear este elemento que, además, es extremadamente versátil, ya que se puede utilizar para fabricar desde pequeños maceteros a grandes rascacielos (como la torre de 1.000 metros de altura que se construye actualmente en Arabia Saudita), lo que permite utilizarlo en una amplia gama de proyectos.
Otra de las características del hormigón es que es posible moldearlo a través de encofrados para así, crear los elementos que darán forma ya sea los distintos elementos. Además, es en este proceso en que se descubre uno de los aspectos clave del material: su gran desempeño estructural.
Si bien el hormigón posee una alta resistencia a la compresión, la que se manifiesta con elementos ya moldeados en encofrados, su desempeño a frente a la tracción es más bien bajo. Aquí, entra el apoyo del acero con barras de refuerzo -lo que se conoce como hormigón armado- y, de esta manera, construir estructuras que mejoren el comportamiento estructural del material y que puedan, por ejemplo, resistir la acción de sismos de alta intensidad sin ver comprometida su integridad.
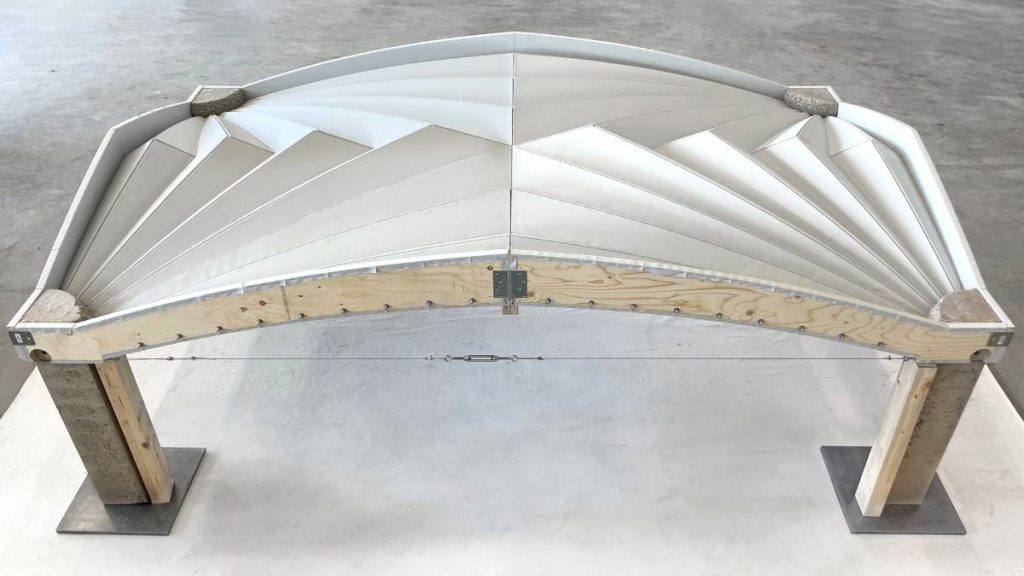
El gran inconveniente de esto es que se requiere de una gran cantidad de material para producirlo, lo que va en la dirección opuesta a las metas de carbono neutralidad que la misma industria del cemento y del hormigón se fijó en sendos documentos tipo Hoja de Ruta. Por lo mismo, un equipo del Block Research Group de la prestigiosa Escuela Politécnica Federal de Zúrich (ETH Zürich), liderado por el profesor Phillippe Block, arquitecto y Doctor en Tecnología de la Edificación del MIT, creó un nuevo tipo de encofrado reutilizable que, por su forma abovedada, sería clave para el desarrollo de una construcción sustentable.
Desarrollando el concepto de “Unfold Form”
El nuevo encofrado para elementos de hormigón, denominado como “Unfold Form” (o “Molde Desplegado”), es una creación de Lotte Scheder-Bieschin, ingeniera civil, integrante del equipo del profesor Block y candidata a doctorado en el ETH Zürich. La premisa de este encofrado es sencilla y se basa en geometría especial para crear elementos de hormigón abovedados -en este caso, pisos de hormigón- que, sin embargo, mantengan la misma estabilidad estructural que el hormigón armado, pero utilizando menos hormigón y acero.
Uno de los inconvenientes al momento de desarrollar este nuevo encofrado es que, al tratarse de geometrías particulares, generalmente son de un único uso, “lo que desafortunadamente, anula algunos de los avances en materia de sostenibilidad”, explicó Scheder-Bieschin.
La solución a ese desafío fue sencilla: el “Unfold Form” se compone de tiras de madera terciada flexibles que se conectan entre sí a través de bisagras textiles, permitiendo que el encofrado se despliegue como si fuese un abanico. De acuerdo con el comunicado de prensa del ETH Zürich, cuatro de estas unidades compactas se pueden ensamblar rápidamente sobre un marco de madera para crear un molde resistente en forma de zigzag sobre el que se puede verter el hormigón directamente.
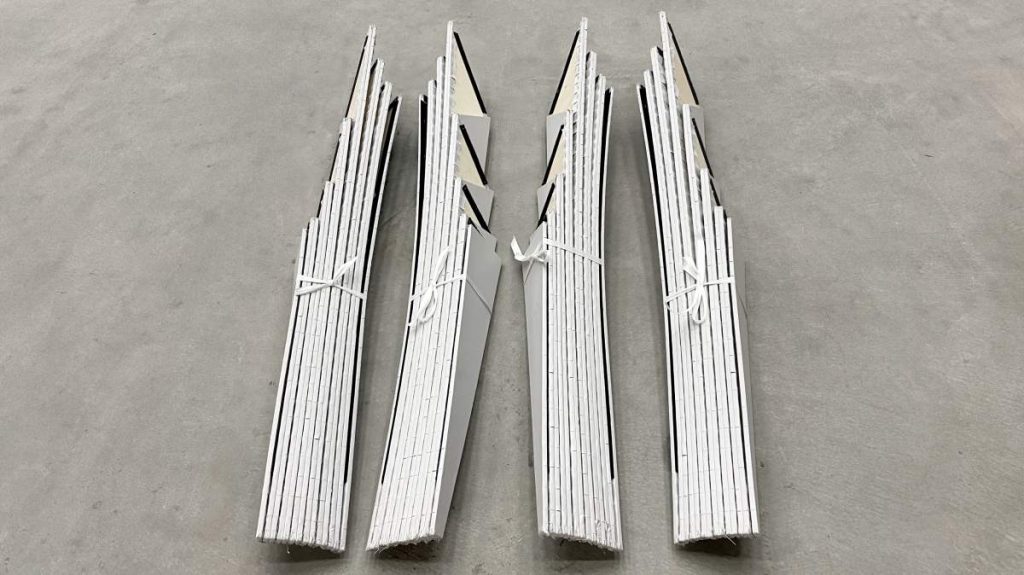
La forma en zigzag de las tiras de madera terciada es la clave de este encofrado para que se mantenga el desempeño estructural del hormigón. “Estas nervaduras entregan rigidez adicional sin aumentar significativamente el peso total”, explicó la ingeniera. “Puedes encontrar este tipo de estructuras articuladas en la naturaleza, como en las conchas de los caracoles de mar”, dijo.
Ese patrón es el que refuerza tanto al encofrado como al hormigón que se vierte en éste. “El hormigón incorpora este diseño a un patrón de nervaduras estructurales, que ayudan en la transferencia de carga”, detalló la candidata a doctorado.
Una vez curado el hormigón, el encofrado se puede desmontar fácilmente desde abajo, plegarlo y guardarlo para un próximo uso. Y si bien el prototipo que se utilizó para ensayos pesa sólo 24 kilogramos, puede soportar hasta una tonelada de hormigón.
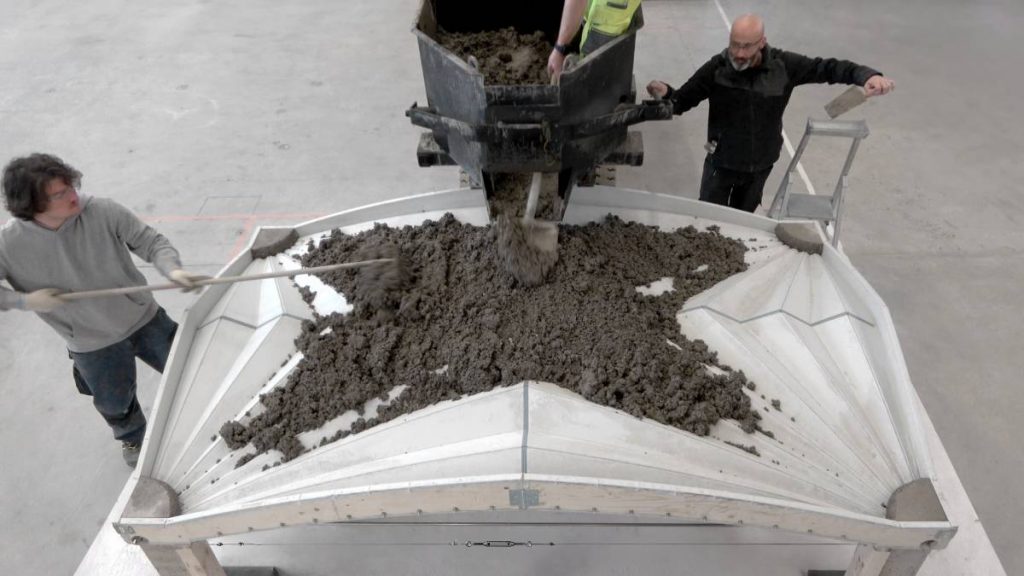
Aplicaciones actuales y futuras del nuevo encofrado
“Estaba buscando por una solución que me permitiese aprovechar la resistencia (del hormigón) a través de la geometría, no sólo para optimizar la estructura final sino también al encofrado en sí mismo”, explicó Lotte Scheder-Bieschin. “Este enfoque reduce el uso de material y hace que el proceso completo sea más amigable con el medioambiente”, agregó. Y es que, de acuerdo con los ensayos, la geometría distintiva del encofrado permite disminuciones de hasta un 60% de hormigón y un 90% de acero, sin comprometer su resistencia estructural.
Otro de los aspectos que Scheder-Bieschin destaca de “Unfold Form” es que no necesita de equipos de alta tecnología ni de operadores especializados tanto para su fabricación como manejo en obra, que es una de las barreras cuando se utilizan encofrados especiales para fabricar elementos de hormigón con formas no usuales. “Esto genera barreras para la construcción sostenible, especialmente en países en vías de desarrollo, donde la necesidad de nuevas edificaciones es alta”, aseveró la ingeniera civil.
Para probar la eficacia de “Unfold Form” se desarrollaron dos prototipos de 3 x 1,8 metros. Uno se encuentra en el Laboratorio de Fabricación Robótica (RFL, en sus siglas en inglés), en el campus Hönggeberg del ETH Zürich, mientras que el otro se transportó a Sudáfrica, específicamente a Ciudad del Cabo, donde en asociación con una empresa local, ensayaron in situ el nuevo moldaje. Con esto, se demostró que este nuevo sistema es reutilizable, es fácil de transportar y trabaja con tipos de hormigón de diferente calidad.
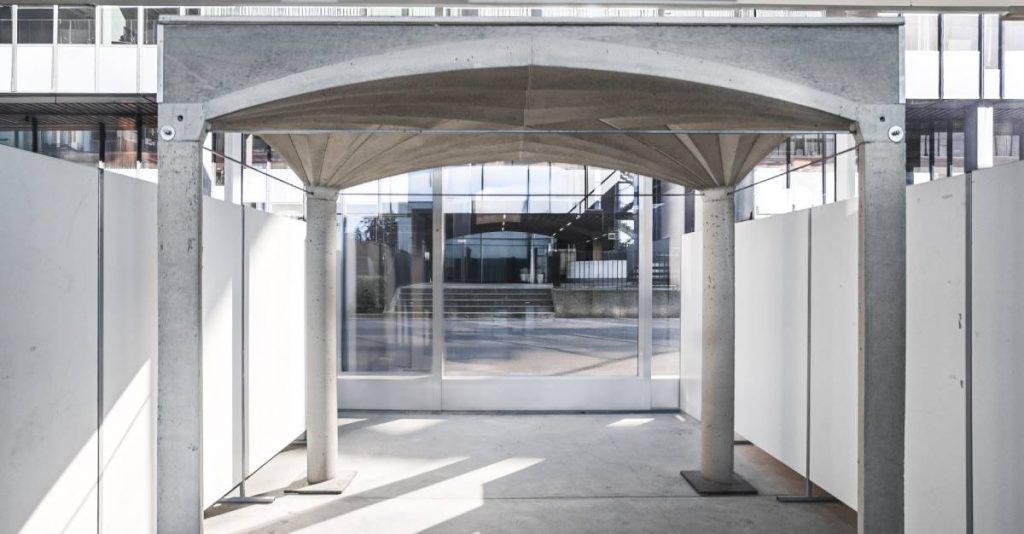
Si bien Lotte Scheder-Bieschin continuará desarrollando la técnica detrás del encofrado “Unfold Form” para sus estudios de postdoctorado, la idea es poner pronto a disposición este sistema. Por lo pronto, la ingeniera civil ejecutó un proyecto en Ciudad del Cabo -el diseño de un mercado- utilizando “Unfold Form”, aunque el próximo paso, comentó es “capacitar a trabajadores locales para que puedan construir ellos mismos el molde y fabriquen sus propias edificaciones”.